Hydrophones are a special class of microphones designed to record underwater audio and as such are an essential tool for research in a variety of disciplines. Uses of hydrophones include the tracking of migratory marine species such as whales, the monitoring of seismic activity, and the monitoring of human marine noise pollution. Arrays of hydrophones are often constructed for marine research in order to more accurately record the intensity and direction of sound and to measure how sounds travel across the ocean. However, marine research projects are often hampered by the expense of hydrophones, particularly if they require the use of several hydrophones in an array, with an average hydrophone costing approximately $600 USD.
The aim of this BPhil project was to explore the potential use of the Vesper VM1000 piezoelectric MEMS microphone as a low-cost alternative to larger, more expensive traditional hydrophones. The VM1000 has several properties that would make it useful for marine research; it is small, thereby allowing it to be used in dense microphone arrays; it is inexpensive, costing $1.49 USD each (when 10 are purchased); and it requires little power to operate, 297μW with a current draw of 165 μA.

At the time of the project’s commencement the VM1000 had not yet been integrated into any commercially available circuit boards. Thus the main steps for this project were:
- Create a working prototype using veroboard.
Design and commission a PCB.
Assemble PCB.
Test the microphone’s frequency response in air and water.
The first stage of the project was relatively straightforward, with the prototype achieving reasonable results when tested with an oscilloscope.
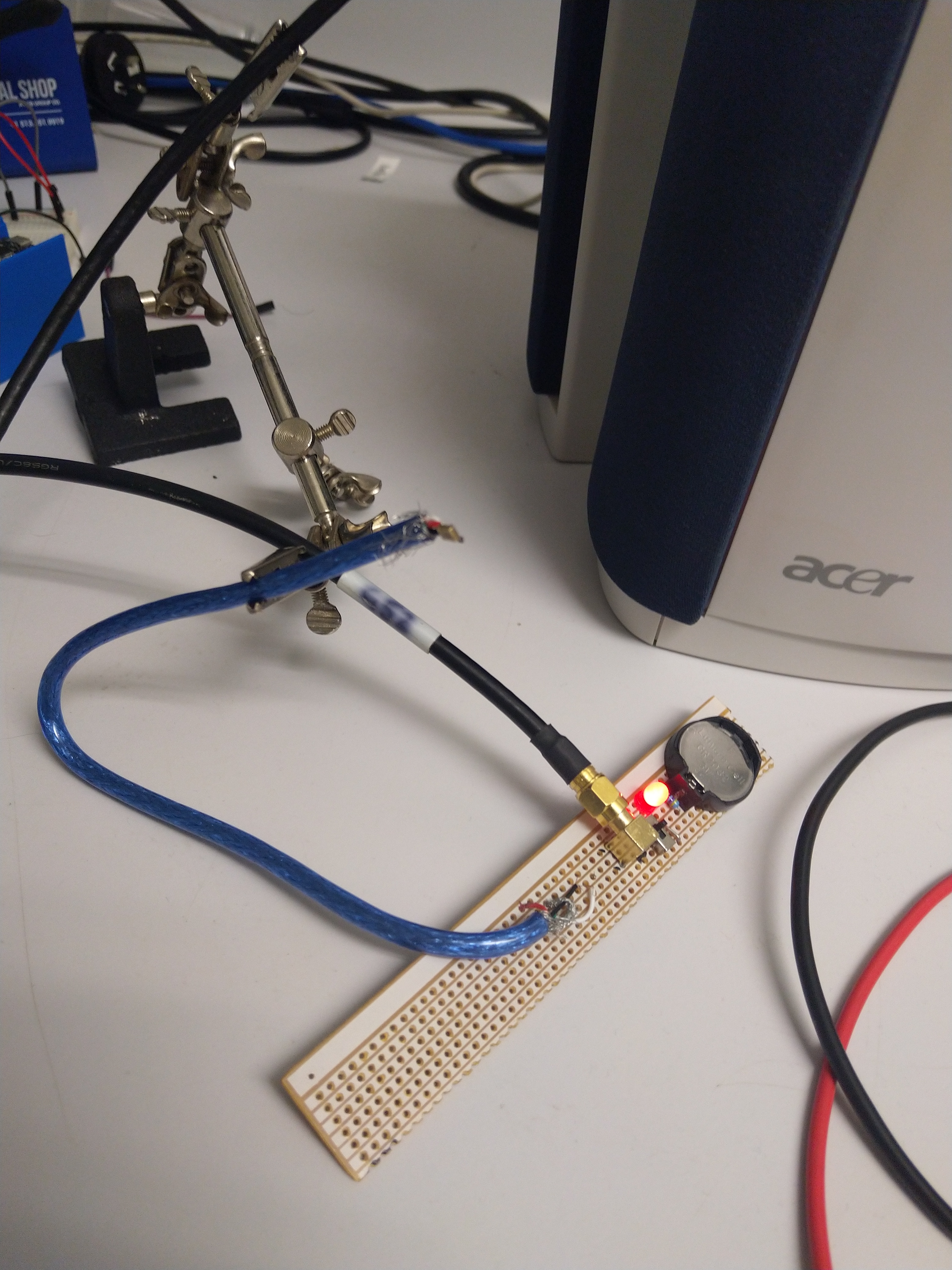
The PCB design phase was also relatively straightforward, though some through-hole components were used in the design as they were on hand. However, this choice was potentially unwise in the long-term as it prevented the PCB from being thoroughly waterproofed and fully tested.
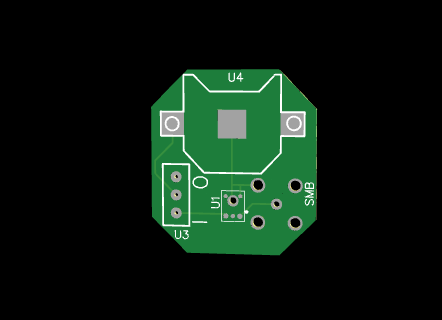
The assembly phase proved challenging as the VM1000 is a surface-mounted component with six small pads that required soldering. This resulted in several microphones being damaged before a successful prototype was produced.
Finally, the testing phase was not completed due to a lack of time, however recommendations for future work are available in the Google Colab document that accompanies this project.
The Colab document, which contains further details about this project was carried out, the design choices made and recommendations for future work can be found here.
Eddie Atkinson completed his BPhil research placement at SHL in Semester 1 of 2019 under the supervision of Ben Travaglione and Melinda Hodkiewicz.